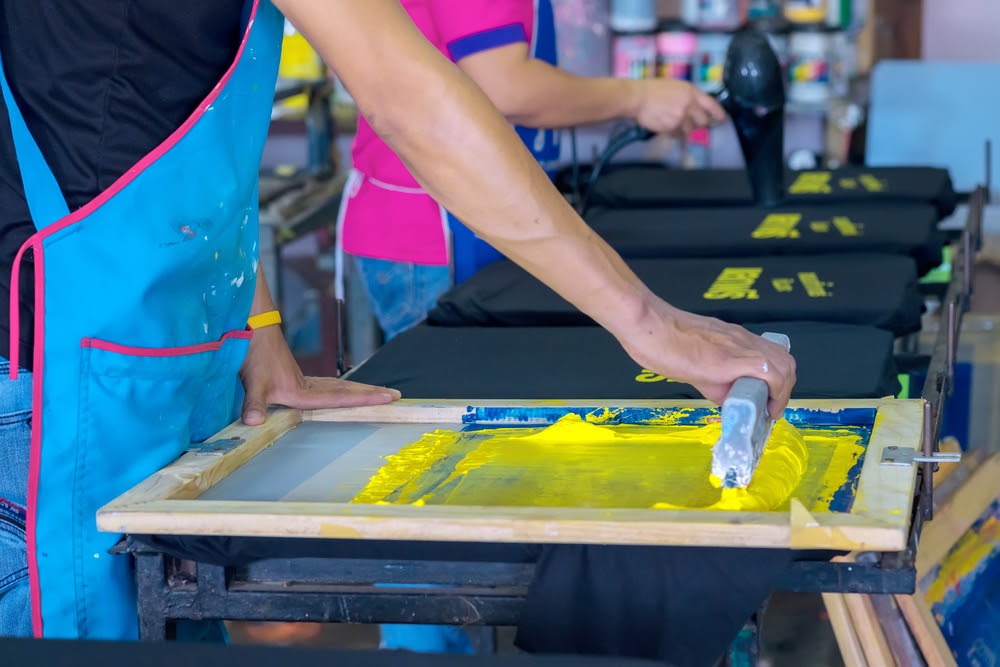
Getting your Trinity Audio player ready...
|
Learn how to screen print and bring your designs to life!
Screen printing is a clever but amazing way of printing different designs on different items like t-shirts, hoodies, even teamwear to stand out from the crowd. It is popular among an extensive array of industries and is used for making bold posters, artwork, and canvases.
But that is not even the best part about this amazing technique. The best part about screen printing is that you can do it at home. You can create all sorts of custom hoodies, and other items of clothing from your living room, garage, or wherever you choose to work. In this guide for beginners, we covered a step-by-step tutorial to screen printing. So keep reading if you want to know how to screenprint shirts, or whatever it is that you wish to print:
What Is Screen Printing?
Screen printing is a printing method characterised by the use of a mesh to transfer ink on a substrate except for the areas. A blocking stencil makes the areas immune. With a very long history (1), screen printing is also known as silkscreen printing, serigraph printing, and serigraphy.
Fabric and paper are commonly used to bring screen printing designs to life. You can print on wood, metal, glass, and plastic with specialised inks. Not just that, you can use screen printing for fabricating and patterning OLEDs (2). We have curated an easy-to-follow guide to screen printing at home. Continue reading if you want to know how to screen print shirts:
Screen Printing Techniques
Once you start learning how to screen print, you will see that they are many different types of screen printing. Some of the most widely used techniques are:
- Metallic Ink Screen Printing
- Glow In The Dark Ink Screen Printing
- Water-based Screen Printing
- Puff Ink Screen Printing
- Reflective Ink Screen Printing
- Discharge Screen Printing
- Foil Ink Screen Printing
- Jumbo Sized Screen Printing
How Does Screen Printing Work: Step-by-Step Guide
Yes, there are many different techniques, but the basic technique is the same, so the methods will not confuse you. The technique we are going to focus on involves the use of a special light-reactive emulsion to make a custom stencil. Lets breakdown how to screen print on fabric step by step:
1. Design Creation
The first thing you need to do if you want to do screen printing at home is to create a design. In order to do so, your printer will take that design and print it on a transparent acetate film. This design is what you will use to make the stencil.
2. Screen Prep
Before you move forward with your screen printing, you must know how to make a screen for screen printing. Once, you have the design, your printer will select a mesh screen to complement the complexity of your design, and your screen printing paper, or fabric’s texture. Afterwards, a light-reactive emulsion will coat the mesh screen. A light reactive emulsion hardens when it develops in bright light.
3. Exposure of Emulsion
Now, you will have to lay the acetate sheet featuring the design on the emulsion-coated screen, and expose it to very bright light. The light will harden the emulsion, and the parts of the screen covered by the design will remain liquid.
If your final design has multiple colours, then you will have to, use a separate screen to apply each layer of ink. For multi-coloured products, a printer uses its skill to design each stencil, and then lines them up perfectly to create a seamless design.
4. Stencil Creation
Once you notice, that the exposed parts of the design are hard, you will need to rinse the liquid emulsion. This will leave a distinct imprint of the design on the screen to let the ink pass through.
Then you will dry the screen and let the printer do necessary touch-ups or corrections to make your imprint as accurate as possible to your original design. After this step, your stencil will be ready for use.
5. Item Preparation for Print
After placing the screen on the printing press, you will lay down your item flat on the printing board under the screen.
You can choose from different presses like automatic and manual styles, but if you choose a modern commercial printer, then remember that it will use an automatic rotary carousel printer. This lets multiple screens to work simultaneously.
6. Pressing Ink on the Item Through the Screen
Now you will lower the screen on the printing board. Then you’ll add the ink to the top end of screen, and spread the ink on the screen’s full length. This will press the ink through the stencil’s open areas and imprint the design on the item underneath.
If your printer is creating multiple items, then you will have to, raise the screen and add a new garment on the printing board and repeat the procedure. Use a special washing fluid to remove the emulsion as soon as printing completes. Why? To use the mesh, to make new stencils.
7. Drying the Product and Checking It
In the end, you will pass the printed item through a dryer. The dryer will cure the ink and create a smooth, colour-fast finished item. You will require to check and wash it thoroughly, before passing it on to its new owner. And your screen-printed item will be complete.
Also Read: The Complete Guide to Sublimation Printing
Tips for the Best DIY Screen Printing
- Opt for high dpi screens because they deliver better detail and significantly enhance the prints. This looks extremely good when you are designing vibrant totes and bags.
- If you do not have access to a dryer, when screen printing at home, for the heat setting, cover your print with paper and iron it for a minute or so.
- If you are using a dark material to print clothes, such as teamwear, then search for ink, with a super opaque label to get a brighter colour print.
- Ask someone to hold your frame for you so you can use both of your hands to pull the squeegee evenly.
Suggested Read: T Shirt Printing DTG Vs Screen Printing
The Final Takeaway
Screen printing has seen many developments and is now used for commercial printing as an artistic medium. You can use one stencil to come up with hundreds of screen printing designs.
Follow our guide to get your head around the procedure of screen printing whatever you want, you can create custom printed T-shirts, sweatshirts, hoodies, totes and bags to give a personal touch to your clothes. Plus, screen printing is the best way to create large orders of custom clothing.
Also Read:
References
(1) Griffiths, Antony. Prints and printmaking: an introduction to the history and techniques. Univ of California Press, 1996.
(2) Pardo, Dino A., Ghassan E. Jabbour, and Nasser Peyghambarian. “Application of screen printing in the fabrication of organic light‐emitting devices.” Advanced Materials 12, no. 17 (2000): 1249-1252.